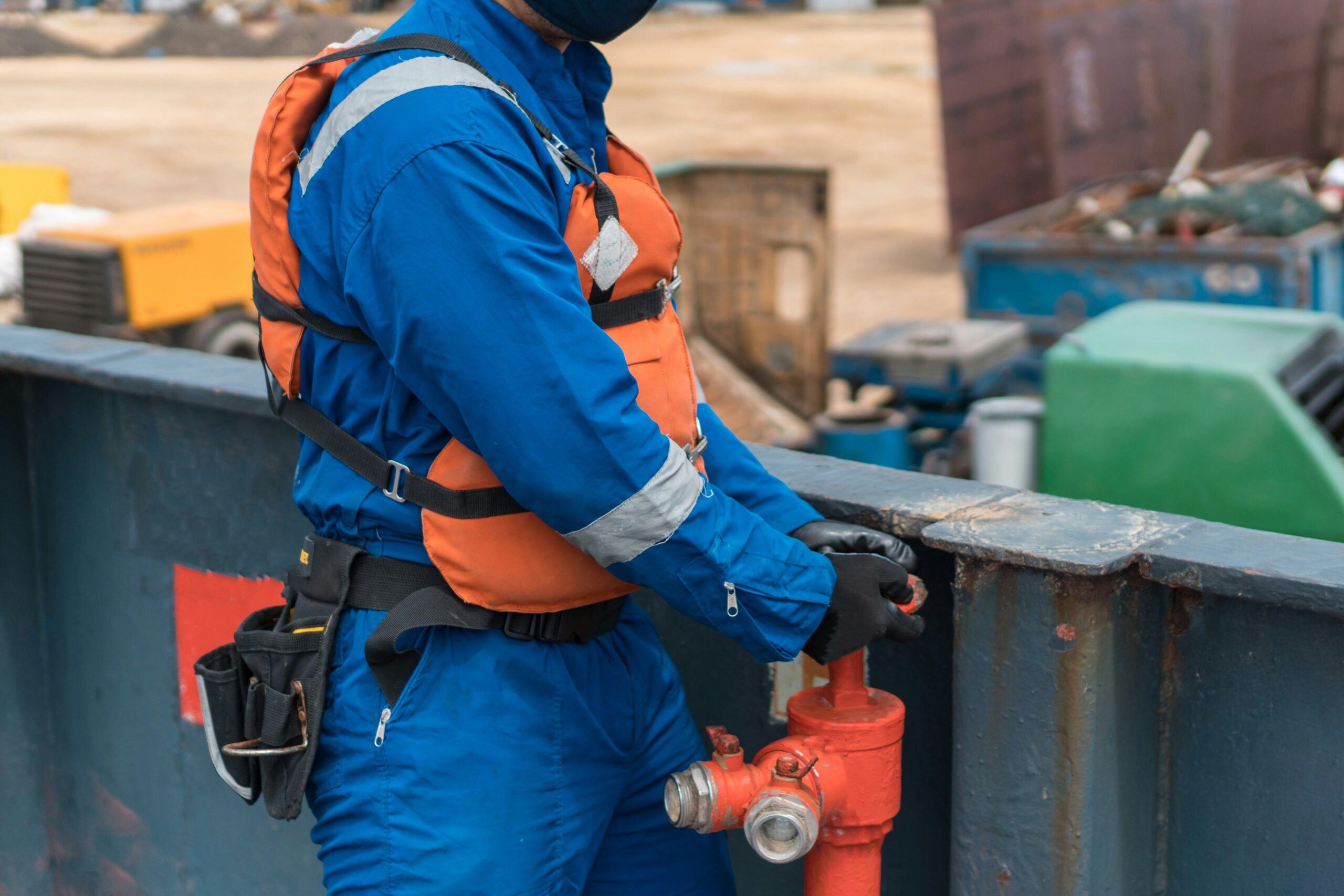
The fusion of technology and traditional industries often leads to remarkable innovations, and one such story is the rise of drilling fluids experts in the tech world. While the drilling industry has always relied heavily on complex engineering solutions, advancements in technology have opened up new frontiers, transforming how drilling fluids are used and managed. A drilling fluids engineer’s expertise is no longer confined to the oil fields. Still, it has expanded into high-tech solutions that enhance operational efficiency, safety, and sustainability. Integrating intelligent systems into drilling fluid management is a game-changer, providing engineers with real-time data and the ability to make precise, data-driven decisions.
In traditional drilling, engineers focused on ensuring that drilling fluids maintained optimal performance under challenging conditions. Drilling fluids are crucial because they help lubricate the drill bit, remove rock cuttings, and regulate pressure within the well. These tasks are vital to the success of drilling operations. However, with the rise of digital tools and data analytics, engineers have been able to monitor fluid performance in real time, optimizing their use for efficiency and environmental sustainability. The evolution of these technologies has turned what was once a manual, reactive process into a proactive, predictive operation.
The Transition from Traditional to Technological Approaches
For many years, drilling fluids engineering was primarily rooted in hands-on methods. Engineers spent their days testing fluid properties and adjusting formulations to meet the specific needs of a well. This was often time-consuming, requiring a deep understanding of the subsurface environment and fluid chemistry. However, as the need for increased productivity grew, the drilling industry began to embrace technology, particularly in sensors, software, and automation systems.
Technological innovation in drilling fluids engineering first emerged with the development of sensors capable of measuring properties such as viscosity, density, and temperature in real time. These sensors allowed engineers to instantly adjust the fluids’ composition, ensuring that drilling operations ran smoothly. As these technologies became more advanced, engineers began integrating machine learning algorithms that could predict future fluid performance based on past data. This reduced the need for manual intervention and improved the accuracy and efficiency of the entire process.
One of the most exciting technological advancements is the development of artificial intelligence (AI) in managing drilling fluids. With AI, engineers can analyze massive datasets to identify patterns and optimize drilling fluids for maximum performance. These systems can predict the behavior of drilling fluids under different conditions, enabling engineers to make better decisions even before a problem arises. The combination of AI, sensors, and real-time data has revolutionized how engineers approach fluid management, reducing downtime, improving efficiency, and lowering costs.
Leveraging Data Analytics for Improved Fluid Performance
Another pivotal change in drilling fluids engineering is using data analytics to optimize fluid performance. As the industry embraces digital tools, engineers increasingly rely on advanced analytics to extract valuable insights from the data generated by sensors and monitoring systems. These insights allow engineers to monitor trends, identify potential issues before escalating, and fine-tune fluid compositions for each job.
Data analytics has enabled the identification of key performance indicators (KPIs) that can be tracked and analyzed over time. By leveraging big data, engineers can better understand how different fluid properties interact under various downhole conditions. For example, by studying the relationship between temperature, pressure, and viscosity, engineers can predict when a particular fluid may fail and make necessary adjustments before any complications arise. Additionally, predictive maintenance has become a key aspect of fluid management, as data can now forecast when equipment will need servicing, reducing the likelihood of unexpected failures.
Moreover, this data-driven approach enhances collaboration across teams. Engineers can share insights with other departments, allowing more efficient coordination between operations and planning teams. This holistic approach optimizes fluid performance throughout the entire lifecycle of a drilling operation, from initial planning to post-operation analysis. Data analytics has propelled drilling fluids engineering into the future, making it a vital component of the tech world.
Enhancing Environmental Sustainability Through Innovation
As environmental regulations scrutinize the drilling industry, drilling fluids engineers have been tasked with finding solutions to minimize its environmental impact. Technological advancements have made it possible to create drilling fluids that are both effective and environmentally friendly. Traditional drilling methods often involve using hazardous chemicals, which pose risks to the environment and human health. However, recent innovations have led to the development of bio-based fluids and systems that reduce the environmental footprint of drilling operations.
The industry has made sustainability a central concern, and engineers now focus on developing eco-friendly alternatives to traditional drilling fluids. Advances in nanotechnology and biochemistry have allowed for the creation of fluids that break down more quickly in the environment, reducing the long-term impact of drilling operations. These eco-friendly fluids help companies comply with environmental regulations and promote corporate social responsibility, which has become a priority for many businesses.
In addition to developing more sustainable fluids, drilling fluids engineers also focus on optimizing fluid recycling processes. Recycling drilling fluids reduces waste and the need for fresh resources, further contributing to sustainability efforts. By utilizing technology to recycle and reuse fluids, the industry is taking a significant step toward reducing its environmental impact while maintaining operational efficiency.
The Future of Drilling Fluids Engineering
The future of drilling fluids engineering lies in further technological integration and the continual pursuit of sustainable solutions. As the industry continues to innovate, the role of drilling fluids engineers will evolve, requiring new skills and expertise. Engineers must stay ahead of the curve by continually learning about emerging technologies and applying them to improve fluid management.
3D printing in drilling fluids engineering may become a reality, allowing for the on-demand creation of specialized fluids tailored to specific drilling conditions. Additionally, developing autonomous systems and robots that can manage fluid composition in real time is on the horizon, further reducing the need for human intervention and increasing operational safety.
The convergence of engineering, data analytics, and technology will continue to drive the drilling industry toward greater efficiency, sustainability, and safety. As drilling fluids engineers take on more high-tech roles, their contributions will be integral to the future of energy production and exploration.
The rise of drilling fluids experts in the tech world highlights the transformative power of innovation. Integrating data analytics, artificial intelligence, and sustainable practices has improved fluid management and enhanced the overall efficiency of drilling operations. As technology continues to shape the future, drilling fluids engineers will play a key role in ensuring that the industry remains at the forefront of operational excellence and environmental responsibility.